Top Packaging Machine Repair Solutions for Enhanced Operational Performance
Wiki Article
The Ultimate Overview to Product Packaging Machine Repair Work: Maintain Your Workflow Running Efficiently
Understanding the intricacies of product packaging maker repair work is essential for maintaining optimum efficiency and reducing disruptions. Normal maintenance not just prolongs the life of these devices but additionally addresses usual issues that can restrain efficiency.Importance of Normal Maintenance
Regular upkeep of packaging equipments is important for guaranteeing optimum performance and long life. By carrying out a structured upkeep schedule, drivers can identify prospective issues prior to they escalate into substantial issues. This aggressive technique not just reduces downtime yet likewise expands the life expectancy of the devices, inevitably leading to lowered functional expenses.Normal inspections allow for the analysis of crucial parts such as sensing units, belts, and seals. Addressing deterioration without delay avoids unanticipated failings that could interrupt manufacturing and lead to expensive repair services. In addition, routine maintenance assists make certain compliance with industry requirements and guidelines, cultivating a safe working atmosphere.
Additionally, upkeep tasks such as calibration, lubrication, and cleaning substantially boost equipment performance. Improved performance translates to consistent product quality, which is important for preserving client fulfillment and brand name track record. A properly maintained product packaging equipment runs at optimum rates and minimizes product waste, adding to general efficiency.
Common Packaging Machine Issues
Product packaging equipments, like any kind of intricate equipment, can come across a range of common issues that might prevent their efficiency and effectiveness - packaging machine repair. One prevalent problem is irregular securing, which can cause item wasting and waste if packages are not properly secured. This commonly results from misaligned components or used securing elementsAn additional constant problem is mechanical jams, which can occur as a result of international objects, used parts, or improper placement. Jams can trigger delays in manufacturing and boost downtime, ultimately influencing general productivity. Furthermore, electronic breakdowns, such as failure in sensing units or control systems, can interrupt operations and lead to imprecise measurements or irregular equipment habits.
Furthermore, problems with product feed can additionally occur, where things may not be supplied to the packaging location regularly, creating interruptions. Wear and tear on rollers and belts can lead to suboptimal efficiency, needing prompt attention to stop more damage.
Comprehending these usual issues is essential for maintaining the integrity of product packaging procedures, guaranteeing that equipment runs efficiently and successfully, which in turn aids in meeting production targets and preserving item top quality.
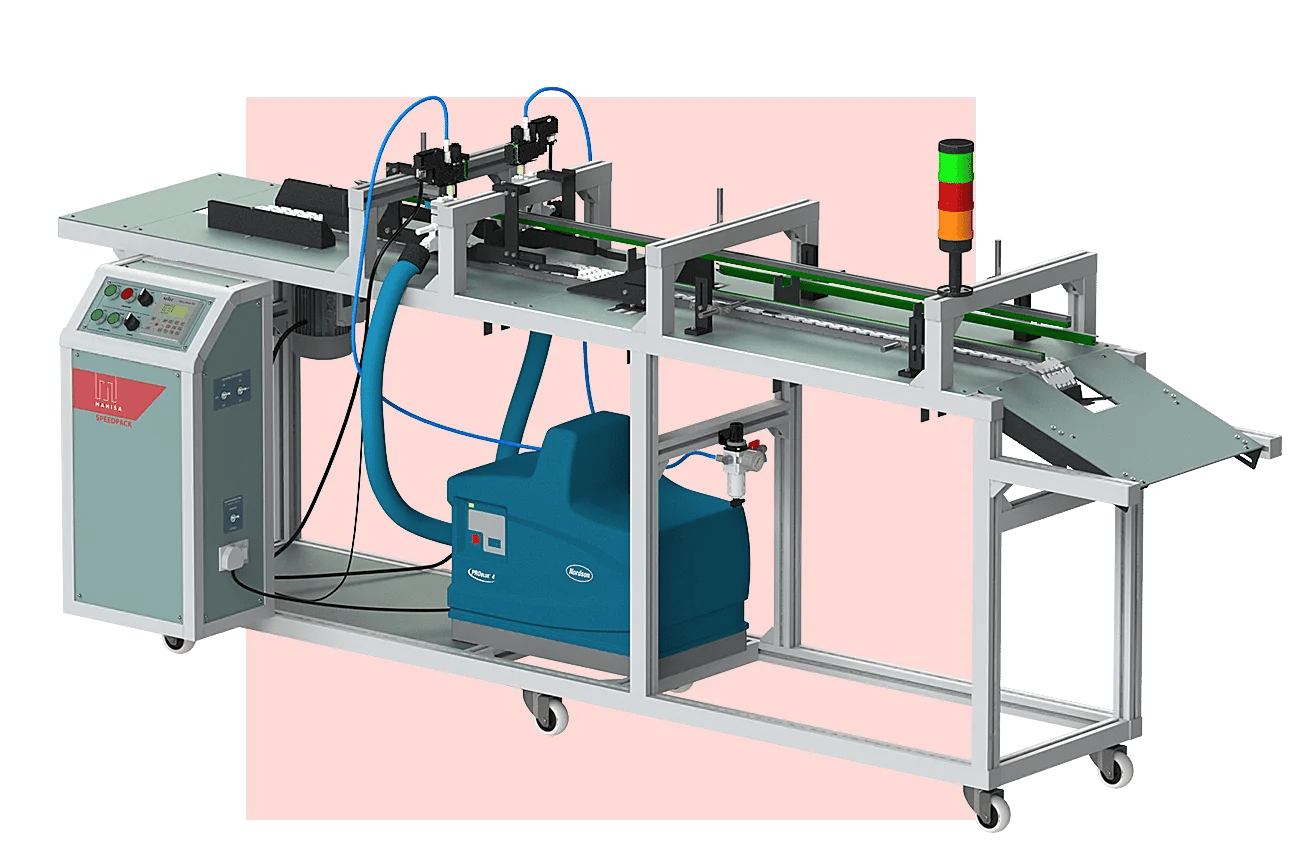
Troubleshooting Strategies
Reliable fixing techniques are essential for without delay attending to problems that arise with product packaging makers. A systematic approach is crucial for determining the root reason of malfunctions and minimizing downtime. Begin by collecting info concerning the signs observed; this may consist of unusual sounds, operational hold-ups, or error codes presented on the device's user interface.Next, describe the device's guidebook for troubleshooting standards particular to the version in concern. This source can offer beneficial insights right into common problems and recommended diagnostic actions. Utilize aesthetic inspections to inspect for loosened connections, used belts, or misaligned parts, as these official source physical elements usually contribute to functional failings.
Execute a procedure of removal by testing private equipment functions. For example, if a seal is not creating correctly, examine the securing mechanism and temperature setups to establish if they meet operational requirements. Document each step taken and the results observed, as this can help in future repairing initiatives.
Repair vs. Replacement Decisions
When confronted with devices malfunctions, choosing whether to replace a product packaging or fix equipment can be a facility and essential selection. This choice rests on a number of crucial elements, including the age of the device, the extent of the damages, and the predicted influence on operational efficiency.
Firstly, consider the equipment's age. Older equipments might need more constant repair services, causing higher cumulative prices that can exceed the investment in a new system. Additionally, review the extent of the malfunction. Minor concerns can commonly be fixed rapidly and cost effectively, whereas considerable damage could require a Source significant economic commitment for repairs.
Operational downtime is an additional important consideration. Investing in a brand-new equipment that offers improved efficiency and dependability could be more prudent if fixing the machine will create prolonged delays. Think about the schedule of components; if substitute components are hard to come by, it may be a lot more critical to replace the machine entirely.
Eventually, doing a cost-benefit evaluation that consists of both long-term and immediate ramifications will help in making a notified choice that straightens with your financial restraints and functional objectives. (packaging machine repair)
Preventative Actions for Long Life
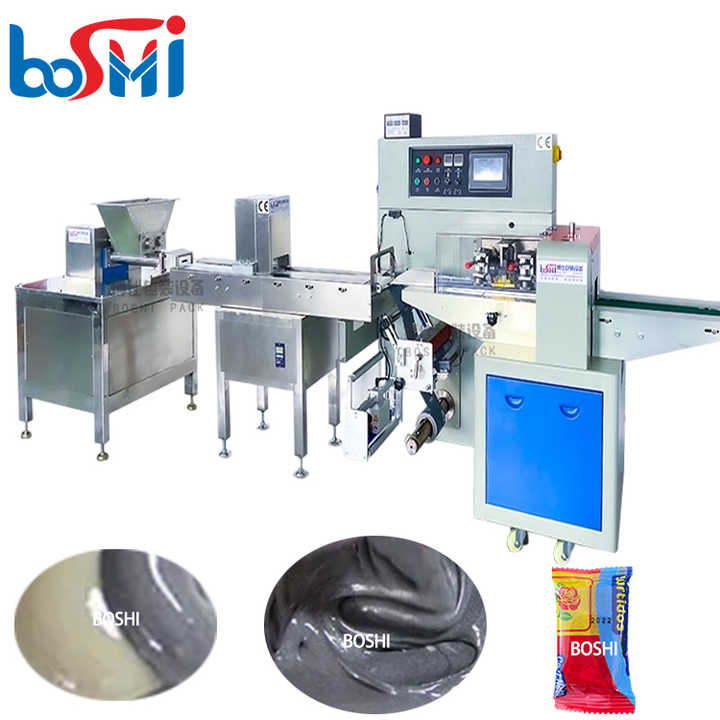
Trick preventative steps include regular lubrication of relocating components, positioning checks, and calibration of controls and sensors. Establishing a cleaning routine to get rid of particles and impurities from machinery can considerably minimize damage (packaging machine repair). In addition, monitoring operational parameters such as temperature and vibration can assist find abnormalities beforehand
Educating team to recognize signs of wear or malfunction is another essential element of precautionary maintenance. Empowering operators with the knowledge to carry out basic troubleshooting can result in quicker resolutions and reduce operational interruptions.
Documentation of maintenance tasks, consisting of solution records and evaluation findings, fosters accountability and facilitates educated decision-making pertaining to replacements and repair work. learn this here now By prioritizing preventative actions, services can ensure their packaging machines run at peak performance, ultimately leading to raised efficiency and decreased operational prices.
Final Thought
In final thought, the reliable maintenance and repair service of product packaging machines are vital for maintaining operational effectiveness. By carrying out preventative steps, services can boost machine durability and make certain undisturbed efficiency in product packaging procedures.Understanding the intricacies of packaging machine repair is essential for preserving optimal efficiency and decreasing interruptions.Normal maintenance of packaging devices is vital for making certain optimal performance and longevity.Packaging machines, like any complicated machinery, can come across a range of typical problems that might impede their performance and effectiveness. If repairing the device will cause prolonged hold-ups, spending in a brand-new maker that uses improved effectiveness and dependability might be more prudent.In verdict, the reliable upkeep and repair service of packaging devices are paramount for maintaining functional effectiveness.
Report this wiki page